Predictive Analytics Ensure Safe Operations for Bristow Fleet
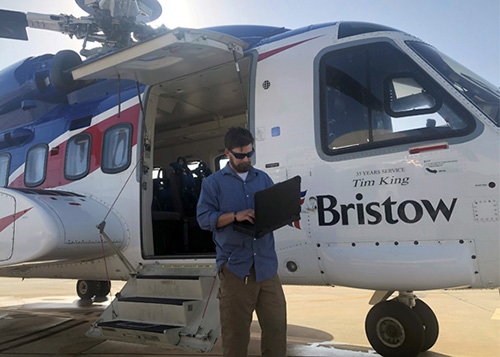
Today, everyone takes for granted that their automobiles smart systems can identify when things are not operating normally. It is the same with our helicopters where sensors can help engineers decide if a part is experiencing some difficulty. The idea is to use predictive analysis to prevent unscheduled maintenance, improve safety and lower costs. The challenge for our maintenance team is to understand what the data is telling us by interpreting it correctly.
One such example of predictive analytics is the information that is pulled daily from the Health & Usage Monitoring Systems or HUMS. On the S-92, the data is pulled after every flight and is imported into the Sikorsky Ground Based Application, or SGBA. Maintenance will perform an analysis, which usually takes about 5 to 20 minutes, and if no issues are found, the aircraft is released back into operations.
The HUMS system will present them with Health Indicators. “If any of those Health Indicators are showing a certain level of vibration has been exceeded on a particular parameter, then the aircraft would be held back from flying until we can understand what the vibration signature is telling us,” said Lee Holland, Fleet Support Manager, at Aberdeen, U.K. “It may require a secondary review of the data or a maintenance action.”
As soon as the battery is switched on, HUMS is activated and starts recording data. It records key activities in the cockpit such as when the pilot starts the engines, when the rotor brake is released, and the gearbox starts moving. “It can become really complex when you start looking at the vibration data and understanding exactly what you are looking at,” Holland said.
The sensors used on the S-92 include accelerometer sensors that measure vibrations. Bristow has been able to use the HUMS data to identify problems by looking at and trending data from the flight. Trending the data can focus on a gradual drift in vibration signatures, rises and falls, step changes or even a data spike – all of these trends require monitoring by a skilled technician. The use of HUMS has become increasingly effective in providing additional data on emerging technical issues.
“Using the SGBA tool, we monitor the fleet and were able to identify an event that led to us change out the accessory gearbox on an S-92. By changing out the part early, it ensures aircraft availability, safety and reliability,” said Rick Bergeron, Maintenance Control Manager, New Iberia, Louisiana.
Engineers noticed a rising trend in vibrations in the righthand hydraulic pump. As noted in the image below, the vibration data showed that it was within safe parameters to keep operating the accessory gearbox, but Bristow by working closely with Sikorsky, decided to replace it. Once the part was replaced, the vibration signature returned to an acceptable level.
“This is a really good example where Bristow and Sikorsky combined their efforts to decide to remove a component from the aircraft prior to it becoming an issue, before there was any unplanned impact to operations. We could see that the vibration signature was increasing, and it was not going to get any better. It is a managed replacement of the accessory gearbox rather than at the end of the flight where we discovered it had risen to an actionable threshold level and had to replace it on an unscheduled basis without prior planning,” Holland said.
“Bristow HUMS limits are lower than OEM limits since we operate on the conservative side,” said Holland. “Even if we had waited, the HUMS system would have eventually initiated the removal of the pump prior to its failure. HUMS does not wait until the component fails, the upper threshold limit implies failure is a possibility. Even though the vibration signature did not reach an alert level, we replaced the accessory gearbox much earlier than would have been required, because predictive analytics worked well and that is a safer way to operate, more economic and efficient.”
“You will get an alert during a flight line level analysis from the software where an exceedance of a threshold occurs, indicating that a vibration signature on a certain component is exceeded. That’s a line level analysis that can be performed quickly,” said Bergeron.
When HUMS goes above the green line, it does not mean that component failure is imminent. “Sometimes it can be that the HUMS Instrumentation is causing the issue or it could be a drive shaft that needs to be re-indexed or it may need a component replacement to correct the root cause of the vibration signature deviation,” Bergeron said. He adds the bottom-line is it takes some investigation to identify the source of the increased vibration and it takes good diagnostic skills to troubleshoot and determine the root cause.
A HUMS specialist can offer additional technical support based off that initial analysis as required, but they also do trending analysis. “Like in this case, you could see the component was in a normal state but then over time it started to trend up, the line engineer notified the HUMS specialist of the rising trend, maintenance actions were initiated, and a recommendation made to replace the auxiliary gear box,” Bergeron said.
“HUMS provides us with non-invasive monitoring of the condition of components we can’t see inside a gearbox,” Holland said. “As HUMS analytics is advancing, more tools are becoming available, one of which is Advanced Anomaly Detection, where existing data it utilized to provide advanced trending capability, identifying early variations in vibration signatures from a particular bearing or gear. It’s all very clever.”
The gearbox is also fitted with a chip detector system, which detects any ferrous particles passing through the oil system. The chip system essentially contains magnets that collect the ferrous particles and completes an electrical circuit, if the debris gets to a certain level, there would be an indication in the cockpit that there is a chip problem. HUMS can warn us of an impending chip detection warning allowing an early intervention and analysis of the debris in the gearbox oil system, Holland added.
“We don’t wait for a gearbox to fail in a helicopter before you perform maintenance. We try to detect any early signs of failure through vibration and debris analysis, which are our primary tools that we rely on daily,” Holland said. “This is in addition to the level of maintenance inspection that you perform on the aircraft such as maintaining the oil system, cleaning and replacing of filters.”
“In addition, the gearbox is inspected periodically by an approved workshop,” Holland said.
HUMS is focused on dynamic components such as gear boxes, engines, drive shafts, and rotor assemblies. HUMS also monitor’s rotor track and balance data, and vibrations introduced into the helicopter through the rotor disk.
The HUMS data is just one area of predictive and proactive analytics on our helicopters, Holland and Bergeron said, but there are other areas such as reliability programs that Bristow uses to keep its fleet operating safely and reliably.
“We use reliability data for maintenance program effectiveness management and are always gathering maintenance and pilot reports from aircraft maintenance operations,” Holland said. The goal is to feed that data into our OEM’s to help decide when maintenance should be carried out and how we can escalate or de-escalate maintenance tasks to improve flight safety and lower our operating costs.
HUMS makes it easier to manage the fleet maintenance before impending or possible problems occur. Holland says HUMS was pioneered by Bristow with its first-time use on the Airbus fleet with it’s SuperPuma helicopters.